Complete Houston Welding Inspection for Improved Efficiency and Sturdiness
Complete Houston Welding Inspection for Improved Efficiency and Sturdiness
Blog Article
The Essential Duty of Welding Evaluation: Understanding the Treatments, Tools, and Criteria That Govern Quality Analysis in Welding Operations
Welding evaluation is an important part of quality control in welding procedures, guaranteeing the architectural honesty and safety and security of welded settings up. By using a range of procedures, from pre-weld evaluations to innovative non-destructive screening strategies, inspectors methodically examine weld quality versus stringent industry standards. The equipment utilized in these processes is crucial for identifying potential flaws that could compromise efficiency. Recognizing the interaction between assessment methods and governing conformity increases essential questions about the obstacles dealt with in keeping these vital methods. What implications do these factors have on the total effectiveness of welding procedures?
Value of Welding Evaluation
Welding evaluation is vital in guaranteeing the stability and safety of bonded structures, as it regularly functions as the last checkpoint before elements are taken into solution. The value of this inspection hinges on its ability to recognize potential defects that might compromise the efficiency and durability of welded joints. Offered the high stakes included, particularly in sectors such as construction, aerospace, and vehicle, comprehensive examination processes are indispensable.
Welding defects can develop from numerous elements, consisting of improper techniques, poor devices, or inappropriate products. Failing to find these issues can cause catastrophic effects, including architectural failings, which might lead to injury, death, and significant financial obligations. Welding assessment provides a methodical strategy to evaluate the quality of welds, making sure conformity with market requirements and regulatory requirements.
Furthermore, reliable welding examination contributes to improving general productivity by lessening rework and making certain that tasks remain on schedule. By fostering a society of quality control, companies can likewise boost their online reputation and client depend on. Essentially, the value of welding inspection can not be overstated, as it plays a critical role in safeguarding both human lives and investments in framework.
Key Examination Procedures
A comprehensive approach to evaluation procedures is crucial for guaranteeing the quality and dependability of welded joints. Effective inspection starts with pre-weld evaluations, which consist of assessing welding requirements, material buildings, and joint designs to identify potential obstacles. This preparation phase develops a standard for quality expectations.
During the welding process, in-process evaluations are essential. Inspectors monitor parameters such as warmth input, traveling speed, and electrode angle to ensure compliance with well-known requirements. Aesthetic evaluations are the initial line of protection, allowing the identification of surface area defects, such as splits, porosity, or incomplete combination.
Post-weld inspections entail advanced strategies to assess the honesty of the joint. This might consist of non-destructive testing (NDT) techniques such as ultrasonic testing, radiographic testing, or magnetic fragment testing. These techniques offer deeper understandings into the internal framework of the weld, disclosing potential flaws that may not show up on the surface area.
Documentation plays an integral role throughout the inspection procedure. In-depth documents of assessments, consisting of findings and restorative activities, guarantee traceability and responsibility, inevitably adding to continual enhancement in welding techniques and total high quality guarantee.
Essential Equipment for Inspection
Effective evaluation relies upon using customized tools made to review the high quality and stability of bonded joints. Key devices in this process include visual assessment devices, such as multiplying glasses and borescopes, which permit examiners to determine surface issues and abnormalities. In addition, ultrasonic testing (UT) devices plays an essential function by utilizing high-frequency audio waves to discover interior imperfections within welds, making sure that concealed weaknesses are recognized prior to they bring about failing.
Radiographic testing (RT) is one more necessary approach, utilizing X-rays or gamma rays to produce photos of the welds, disclosing inner flaws that may not show up via other assessment methods - Houston Welding Inspection. Magnetic fragment testing (MT) is employed for ferromagnetic materials, enabling assessors to find surface and near-surface issues by applying electromagnetic fields and fine fragments
Dye penetrant screening (PT) is also considerable, including the application of a fluorescent dye to expose surface fractures and stoppages. Each of these tools and methods adds to a thorough evaluation strategy, guaranteeing that welded frameworks satisfy the essential top quality requirements and continue to be safe for use in their respective applications.
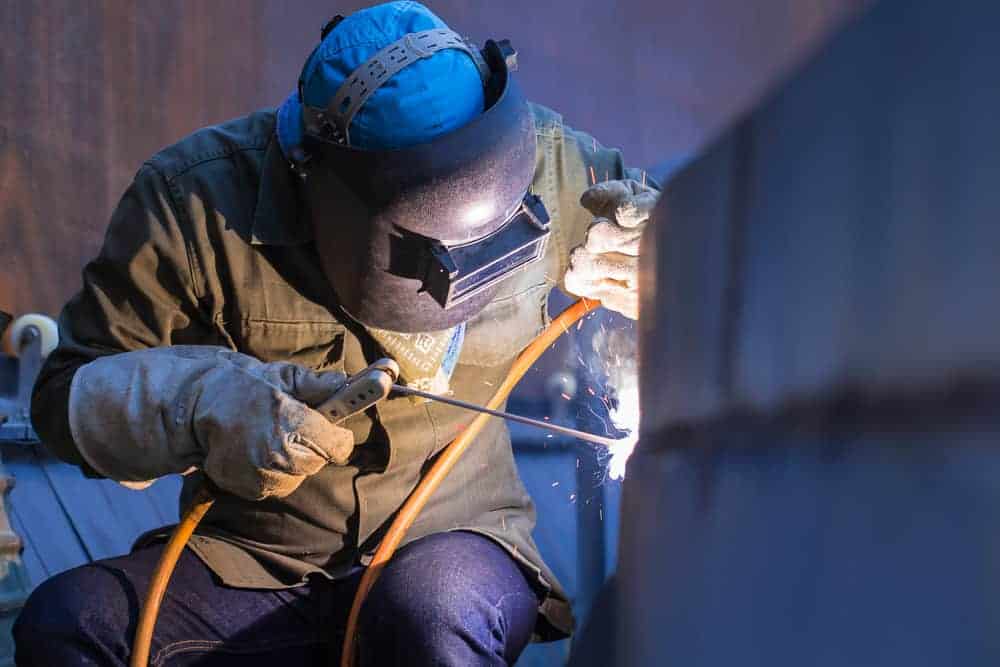
Industry Specifications and Rules
Quality guarantee in welding inspection is substantially affected by industry standards and laws that control practices and ensure safety and security. These standards function as criteria for quality, outlining the necessary protocols for testing, documents, and evaluation. Trick companies such as the American Welding Culture (AWS), the American Culture of Mechanical Designers (ASME), and the International Organization for Standardization (ISO) establish guidelines that welding experts must comply with throughout the evaluation procedure.
Compliance with these standards is not only an issue of regulative responsibility but also an important element of risk management in welding operations. They incorporate different aspects, consisting of product choice, welding methods, and credentials of personnel. AWS D1.1 outlines architectural welding needs, while ISO 3834 defines quality demands for welding processes.
In addition, industry guidelines determine the needed certifications for welding inspectors, demanding qualifications that verify their expertise. This placement with criteria makes certain that examinations are executed consistently and properly, ultimately protecting the honesty of welded frameworks. Sticking to these industry standards and regulations is extremely important in promoting operational efficiency and keeping public count on welding practices.
Difficulties in Welding Evaluation


Welding assessment encounters many click this link challenges that can impact the reliability and safety of welded structures. One significant obstacle is the complexity of the welding processes themselves, which can differ significantly relying on materials, joint arrangements, and ecological problems. This irregularity necessitates an extensive understanding click for more of varied examination strategies and their proper applications.
Another challenge hinges on the developing nature of welding modern technology. As brand-new materials and approaches are presented, inspectors need to constantly upgrade their understanding and abilities to successfully evaluate the top quality of welds. Furthermore, the physical ease of access of weld locations can impede assessment initiatives, especially in restricted or risky settings.
In addition, human variables play a critical role in welding assessment. Houston Welding Inspection. The subjective nature of aesthetic evaluations can cause variances, as various assessors may analyze the very same weld in different ways. This emphasizes the importance of standard training and certification for assessors to make sure an uniform method to quality assessment
Lastly, the integration of innovative modern technologies, such as automated examinations and synthetic intelligence, offers both opportunities and challenges. While these modern technologies can boost precision and effectiveness, they additionally need significant financial investment and know-how to carry out effectively. Addressing these difficulties is important for preserving the honesty of bonded frameworks.
Verdict
Welding inspection is vital for ensuring the safety and security and honesty of welded frameworks. Via extensive analysis procedures, making use of specific tools, and adherence to identified market standards, the high quality of welding procedures can be methodically evaluated. Difficulties continue the evaluation procedure, yet the application of effective techniques can minimize risks related to architectural failings. Ultimately, a robust welding evaluation structure not only ensures conformity with policies however likewise boosts overall operational efficiency and dependability.
Welding assessment is an indispensable component of quality guarantee in welding operations, making sure the structural honesty and security of welded assemblies.Welding examination is vital in ensuring the stability and safety and security of bonded structures, as it frequently offers as the final checkpoint prior to components are put into solution. Welding examination offers an organized approach to assess the quality of welds, ensuring conformity with market standards and regulative needs.
Quality assurance in welding evaluation is significantly affected by sector standards and laws that control techniques and make sure click now safety and security. Trick organizations such as the American Welding Society (AWS), the American Culture of Mechanical Engineers (ASME), and the International Company for Standardization (ISO) establish standards that welding professionals need to stick to throughout the assessment procedure.
Report this page